製品紹介PRODUCT INTRODUCTION
射出成形において品質向上の為には金型技術と成形技術の両方が必要です。試作時には量産の観点から成形上の問題点を洗い出しそれを金型修正で直していきます。量産時に安定した成形を行う為にはしっかりした成形技術が必要です。過去の成形条件の蓄積を元に技術者の教育、標準書類への展開に努めています。
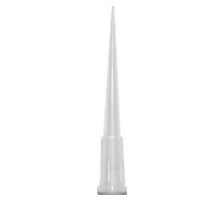
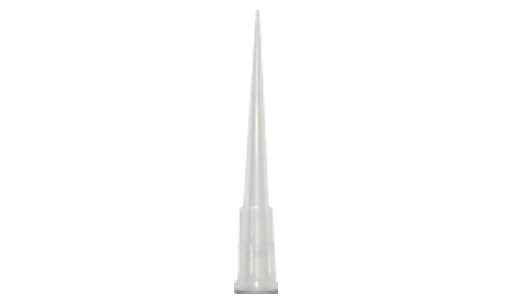
クリーン
医療用検査機に使われる製品ですので、衛生面での高い安全性が要求されます。製造はもちろん梱包に至るまでクリーンな環境での作業が必要で、本社第三工場のクリーンルームで製造を行います。また1回に32ヶと多数の成形を行うことでコストダウン。取数が多くても安定した生産を行うには、金型設計・製作、成形の高度な技術が必要です。

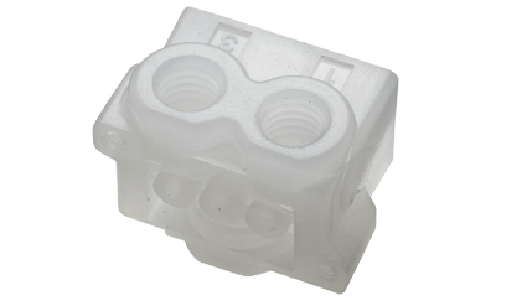
ネジ
金型を使用した射出成形は型に溶かした樹脂を流し込み、型を開くと製品ができているという仕組み。上の写真の製品はネジ穴が四方に空いていますが、これも一度のプラスチック成形でできています。金型を作成する際の型構造の緻密な設計により様々な形状を生み出しています。
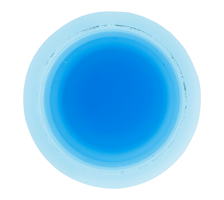
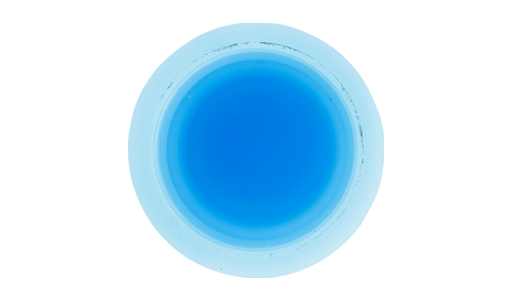
真円度
円、と言葉にするのは簡単ですが、実際の部品でゆがみのない限りなく正確な円を作り出すのは非常に困難です。元になる金型が真円だとしても仕上がる製品はなかなか真円にはなりません。真円度0.01。先端のテクノロジーと熟練した人間の技術によって高水準の製品が仕上げられていきます。
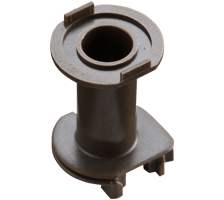
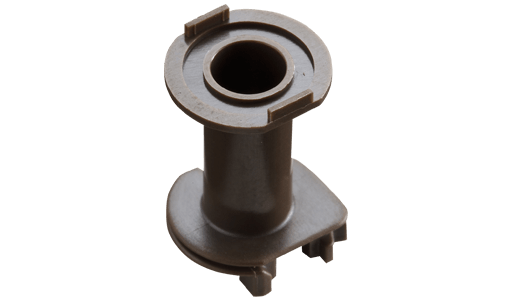
精度
上述の円と同様ですが、求められる精度は製品によって異なります。左の写真の製品の内径では図面上の寸法と実際の製品との間に許される図面公差は±0.01mmでした。当社では金型部、製品部の連携により、こうした高精度の製品を日常的に生み出しているのです。
成形の流れと技術MOLDING FLOW AND TECHNOLOGY
射出成形の製品ができるまでには、大きく分けて、形状の要となる金型の製作、試作、量産の工程があります。
順を追ってプラスチックの成形工程を見てみましょう。
順を追ってプラスチックの成形工程を見てみましょう。
STEP1
金型の製作
製品図を元に取数、ゲート位置、パーティングライン(金型の割り位置をどこにするか)、型寸、型構造などの金型の仕様を決め、その後、CADで型図を作成、各種工作機械により切削加工を行います。写真右はコンピュータ制御の切削加工機、マシニングセンター。写真下は完成した金型です。
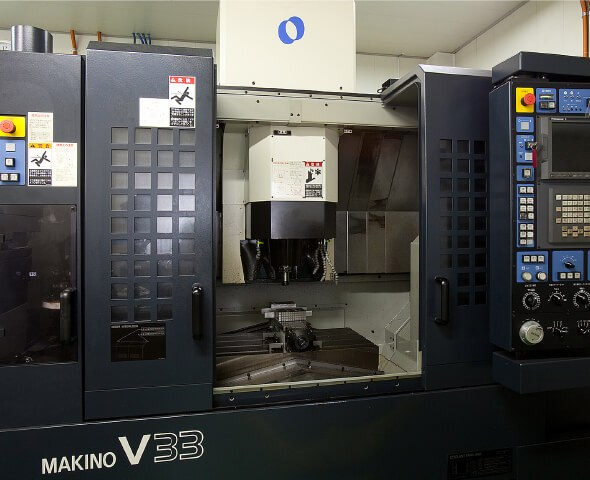
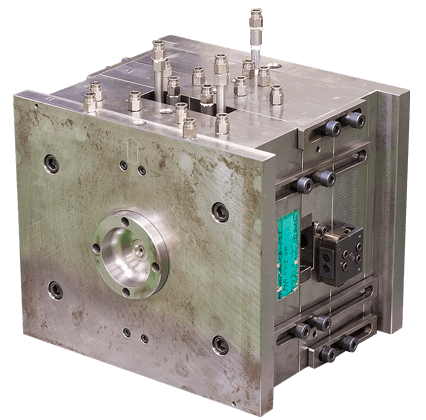

STEP2
試作
製作した金型を射出成形機に取り付け試作を行います(写真左)。試作により成形上の問題点を見つけ出し金型の修正を行い量産できる型に仕上げていきます。また、ミクロン単位の高精度の製品を仕上げるため、三次元測定機などを用いて計測し、金型を調整していきます。
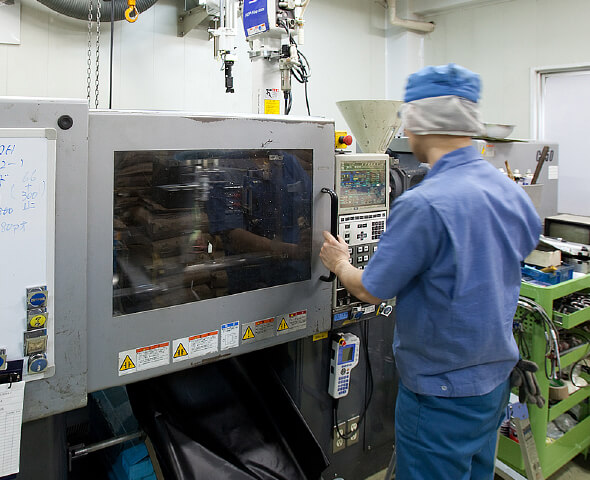


STEP3
全寸法検査(型検)
工具顕微鏡や三次元測定機などを用い、図面と照らし合わせ製品の全寸法の測定を行います。写真右上は三次元測定器。立体の数値データを端末モニタで確認できます。
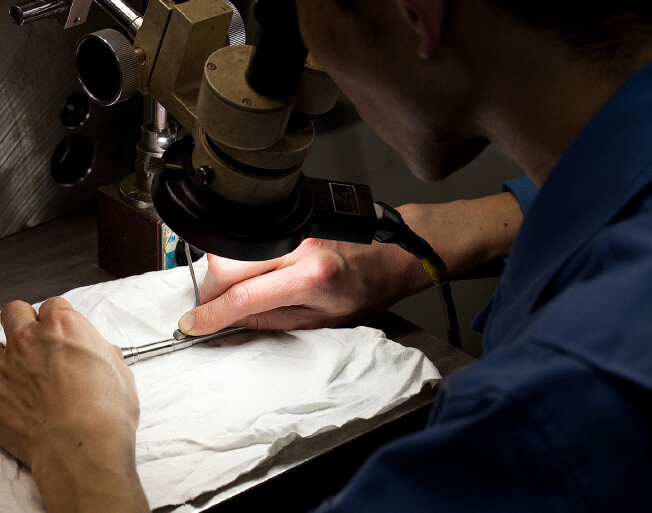
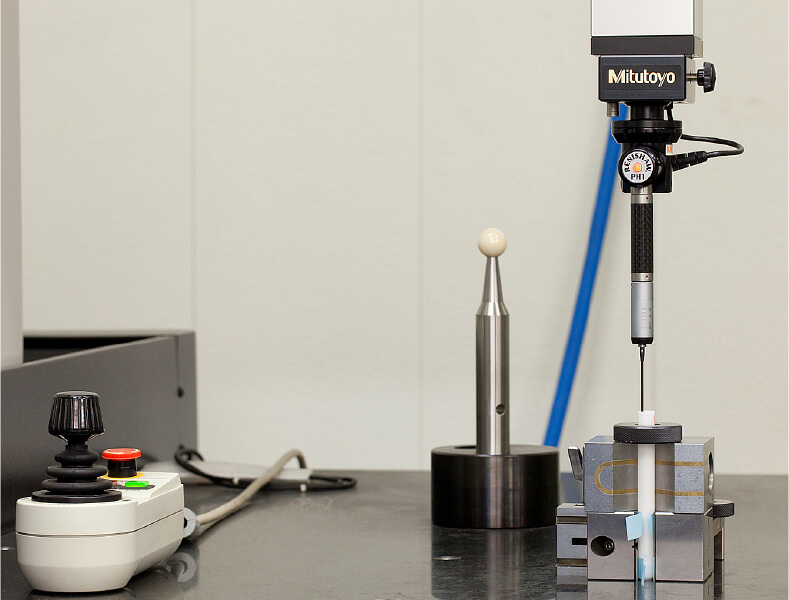
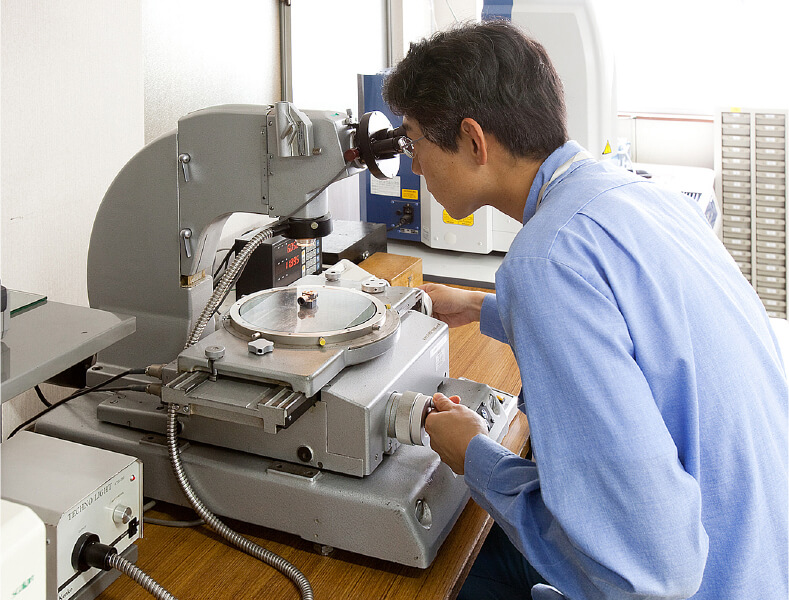

STEP4
量産
射出成形機に金型をセットし、諸条件をコントロールパネルから入力して、量産を行います。ここからはほぼ自動化された工程ですが、一定の時間をおいての抜き取り検査、仕上がった製品の検品には人手もかけて万全を期しています。写真下は第三工場の自動充填検査の様子。
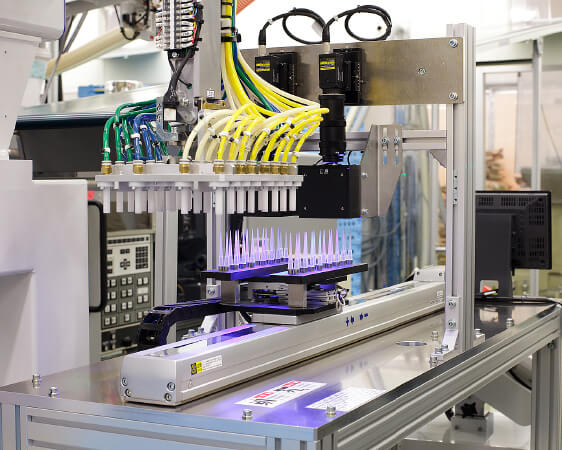
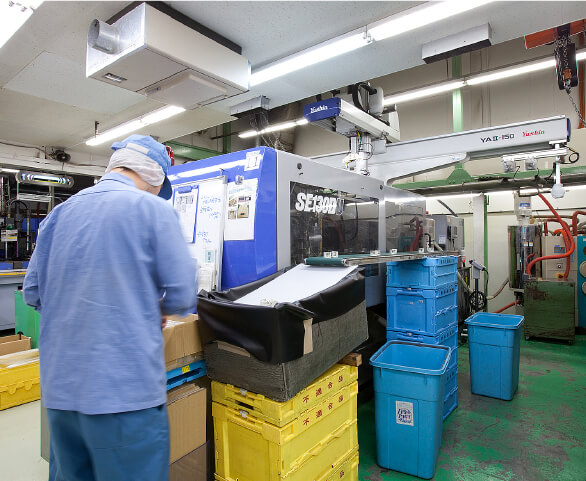
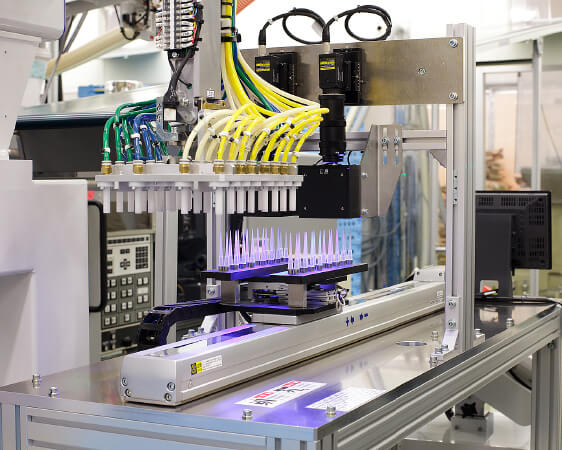
設備一覧EQUIPMENT LIST
- 成形設備台
- 射出成形機
- 横型
- 50t9
- 75t32
- 100t24
- 130t25
- 竪型
- 75t9
- 超音波溶着機12
- 粉砕機100
- 成形監視装置102
- 乾燥機(除湿型含む)101
- アニーリング装置2
- チラー10
- 金型温度調節機99
- 吸湿装置(8kW)2
- 金型・検査設備台
- NC放電加工機1
- マシニングセンター2
- ワイヤー放電加工1
- フライス盤3
- 平面研削盤1
- 旋盤1
- ラジアルボール盤1
- 精密小型旋盤1
- 成形研削盤4
- 3次元測定器1
- 画像処理装置2
- 工具顕微鏡4
- 投影機(600mm)1
- 表面粗さ測定器1
- デジタルフォースゲージ4
- 栓ゲージ等各種ゲージ類約3000本